泰安非标注塑配件定制
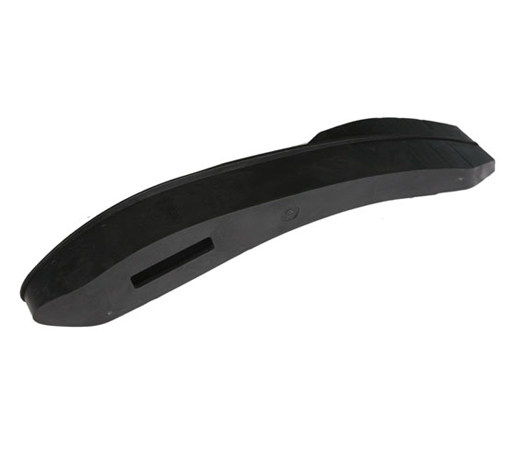
注塑加工对应的常用设备就是注塑机,为了能使其实现高节能、高精度、高应答、低噪音、低油温等特性,需要对其原有的传动系统进行改进,建议采用伺服系统,这样注塑机的使用效果会更高,注塑加工质量也会更高。注塑机以全液压式为主,对于节能及环保的意义并不明显贡献明显较弱,但是换成伺服马达进行注塑加工的话,不仅改善了定量泵液压系统的缺点,而且它的输出流量的大小可以通过精准转速的增减控制来获得,以达到压力精准控制的目的,可大幅降低输出的电力消耗。节能系统主要是由伺服马达、驱动器及油泵组三部分构成,其中伺服马达分为AC感应伺服与永磁式伺服;驱动器的控制技术依据马达特性分为变频控制及伺服控制;油泵类型常见有齿轮泵、柱塞泵、叶片泵,齿轮泵包括外齿轮、内齿轮及螺旋式。
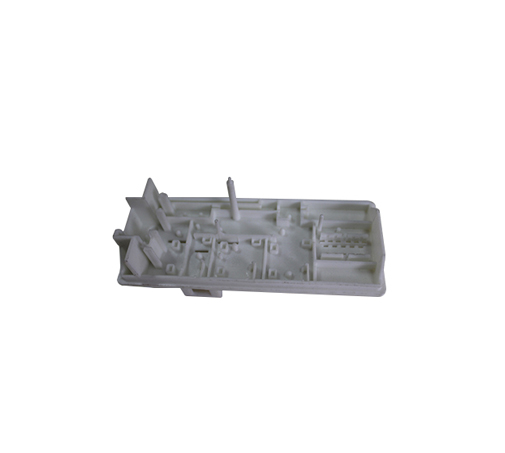
所以必须合理地安排注射、保压和冷却时间,采可以实现注塑加工产品质量和生产率的提高。我们的所说的冷却时间,指的是塑料熔体从充满注塑模具型腔起到可以开模取出制件时止的这一段时间。可以开模取出制件的时间标准,常以制件已充分固化,具有一定强度和刚性为准,在开模顶出时不致变形开裂。非标注塑配件定制即便是用同一种材料进行注塑加工,它的冷却时间也随壁厚、熔融塑料的温度、成型件的脱模温度及注塑模具温度等因素的变化而不同,所以要想百分之百正确地计算出冷却时间还是有一些难度的,只能在适当假定的基础上进行计算。冷却时间有三种参考标准,一种是注塑加工件壁最厚部位中心层的温度,冷却到该塑料的热变形温度以下所需要的时间;另一种是注塑加工件断面内的平均温度,冷却到规定制品的出模温度所要的时间。注塑加工的冷却时间还可以以结晶性塑料成型件壁的厚部分中心层温度为标准,冷却到其熔点以下所需要的时间,或达到规定的结晶化百分比所需的时间。
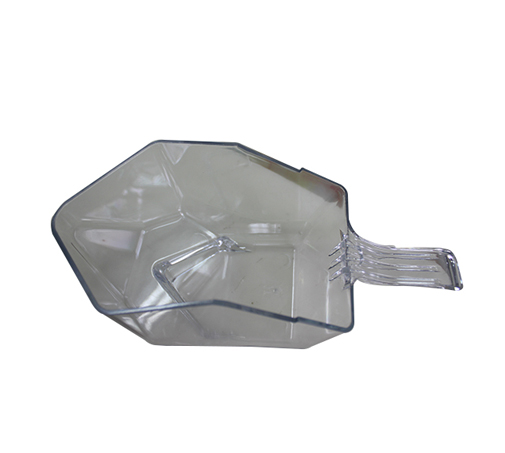
注塑加工工艺对于配料的有效质量标准要求,在注塑机内部的不同位置按照时长的控制,设计不同的配料和用量。注塑加工的时候,可以利用温度传感器对温度进行有效的测量,温度的精确度很高。准确的控制温度才有可能得到优质的注塑产品,使得注塑加工工艺发挥价值。自动化的程序控制可以实现在特定的时间之内,将所需配料进行混合与加工,通过出口位置进行注塑模具的产品制造和加工,从而完成产品的加工和成型。不同的成型方式,要求对于机器不同的用量进行有效的搭配和配合。模具的操作水平以及对各种冲压工艺掌握和运用到位与否,同样也会关系到注塑加工的质量,所以必须严格依据操作规程,使之符合要求和标准。而在实际设计的工作中,还需要大家结合问题的差异性去灵活地采取解决措施。
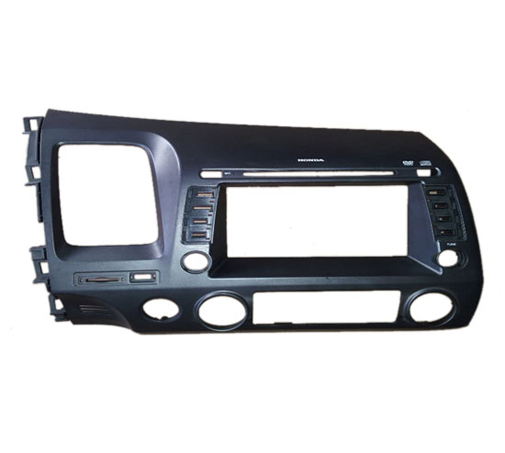
塑料制品的使用越来越多,塑料制品的类型也很多,都得到了普遍的使用。质量取决于加工的控制,加工对塑料制品的影响是比较大的,尤其是在注塑加工是对温度的控制,是很重要也比较难的一步,所以需要特别注意。现在大家跟我们一起来了解一下注塑加工对温度的控制。充模过程采取的是一维导热,对应的冷却也是一维冷却。在高温流体进入之后,成型后产品的比热容、自身具备的热传导系数都是不变的。在制品成型的过程中,磨具和塑料制件均处于恒定的温度场中。在恒定的温度场中,当中心温度等于塑料热变形时候的温度时,整个冷却周期结束。这也说明了上下限点具有两方面的作用。根据不同的注塑要求,其上下限的温度也是不同的,所以很多情况下都是需要具体问题具体分析。
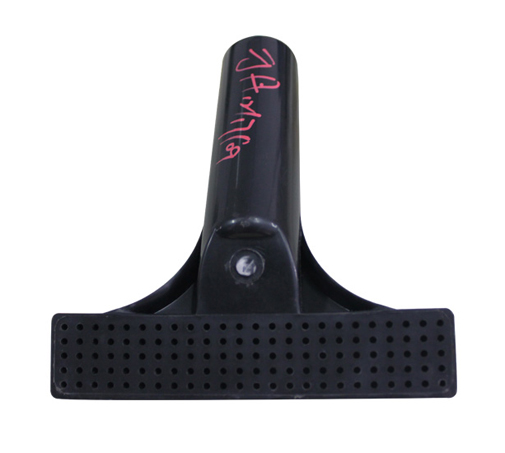
注塑加工中模具加工的精度要求,包括了模具尺寸的制造精度、垂直度、同轴度、平行度等等。一般注塑加工模具尺寸的制造精度应在0.005-0.02mm范围内;而垂直度要求在0.01-0.02mm范围内;同轴度要求在0.01-0.03mm范围内;动、定模分型面的上、下两平面的平行度要求在0.01-0.03mm范围内。注塑加工用模具的滑动部分的配合精度一般选用H7/e6、H7/f7、H7/g6三种,需要注意的是镜面上如有做了挂靠台阶的镶件,那么要求配合不能太紧,否则在镶件从正面往后退敲打时用来敲打的工具易碰坏镜面,在不影响产品尺寸的情况下,可取双边0.01~0.02mm的间隙配合。 注塑加工的时候,那些还要热处理加工的工件,要求其热处理前外形备料尺寸单边加0.25mm的磨床余量;而对于模仁、镶件需要CNC粗加工的部分,单边预留余量0.2mm,要知道这合理的预留量也会影响工件的精确度。
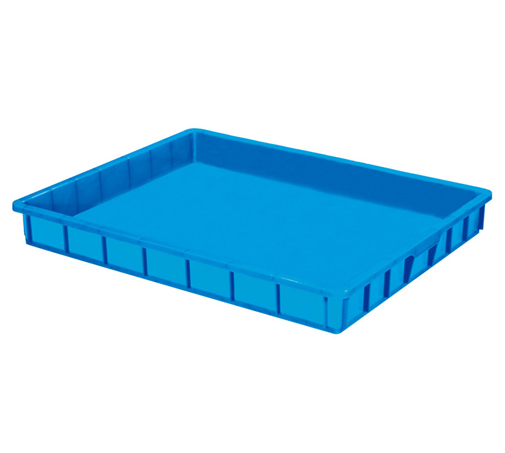
一次注塑模塑过程所需的时间定义为成型周期,这一参数将直接影响注塑加工的生产下来和设备的利用率。因此,要尽量做到在保证质量的前提下,缩短注塑加工的成型周期。成型周期实际上是由各个有关时间构成的,其中较为重要的是注射时间和冷却时间,因为这两大参数会对注塑加工制品的质量起到决定性的作用。以注射时间来说,具体还将涉及到充模时间、保压时间等。注塑加工成型周期的冷却时间主要决定于制品的厚度、塑料的热性能和结晶性能,以及模具温等诸多因素。但不管时间长短,都要以保证制品脱模时不引起变动为原则,基本上控制在30-120秒钟之间。没有必要延长其冷却时间,不然不仅降低生产效率,对复杂制件还将造成脱模困难,而强行脱模时甚至会产生脱模应力。