潍坊哪里有塑料件制品生产厂家
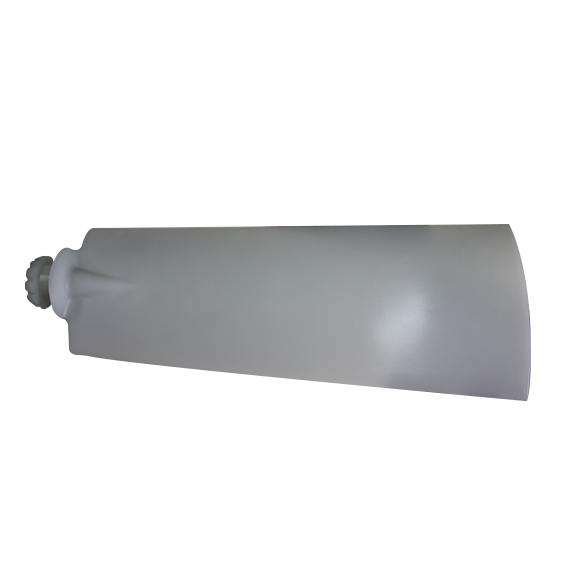
注塑加工中模具加工的精度要求,包括了模具尺寸的制造精度、垂直度、同轴度、平行度等等。一般注塑加工模具尺寸的制造精度应在0.005-0.02mm范围内;而垂直度要求在0.01-0.02mm范围内;同轴度要求在0.01-0.03mm范围内;动、定模分型面的上、下两平面的平行度要求在0.01-0.03mm范围内。哪里有塑料件制品生产厂家注塑加工用模具的滑动部分的配合精度一般选用H7/e6、H7/f7、H7/g6三种,需要注意的是镜面上如有做了挂靠台阶的镶件,那么要求配合不能太紧,否则在镶件从正面往后退敲打时用来敲打的工具易碰坏镜面,在不影响产品尺寸的情况下,可取双边0.01~0.02mm的间隙配合。 注塑加工的时候,那些还要热处理加工的工件,要求其热处理前外形备料尺寸单边加0.25mm的磨床余量;而对于模仁、镶件需要CNC粗加工的部分,单边预留余量0.2mm,要知道这合理的预留量也会影响工件的精确度。
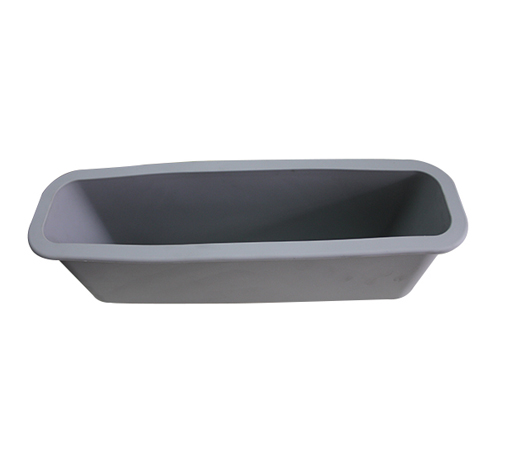
一次注塑模塑过程所需的时间定义为成型周期,这一参数将直接影响注塑加工的生产下来和设备的利用率。因此,要尽量做到在保证质量的前提下,缩短注塑加工的成型周期。成型周期实际上是由各个有关时间构成的,其中较为重要的是注射时间和冷却时间,因为这两大参数会对注塑加工制品的质量起到决定性的作用。以注射时间来说,具体还将涉及到充模时间、保压时间等。注塑加工成型周期的冷却时间主要决定于制品的厚度、塑料的热性能和结晶性能,以及模具温等诸多因素。但不管时间长短,都要以保证制品脱模时不引起变动为原则,基本上控制在30-120秒钟之间。没有必要延长其冷却时间,不然不仅降低生产效率,对复杂制件还将造成脱模困难,而强行脱模时甚至会产生脱模应力。
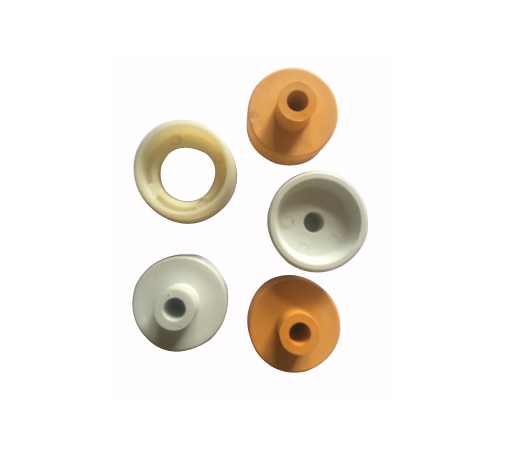
欠注:在塑料加工中,由于型腔填充不满,导致塑件外形残缺不完整的现象。溢料飞边:塑料加工模塑过程中,溢入模具合模面缝隙间并留存在塑件上的剩余料。熔接痕:塑件表面的一种线状痕迹,是由注射或挤出中若干股流料在漠具中分流汇合,熔料在界面处未完全熔合,彼此不能熔接为一体,造成熔合印迹,影响塑件的外观质量及力学性能。波流痕:由于熔料在模具型腔中的不适当流动,导致塑件表而产生年轮状、螺旋状或云雾状的波形凹凸不平的缺陷。皱裂:层压塑料表面产生破裂和明显分开的一种缺陷。皱折:塑料加工过程中,塑件表面一层或多层出现折痕或皱纹的外观缺陷。塑料产品在我们生活中应用的非常广泛,为了扩大塑料制品的应用范围、改善塑料产品的性能,我们需要进行塑料加工。
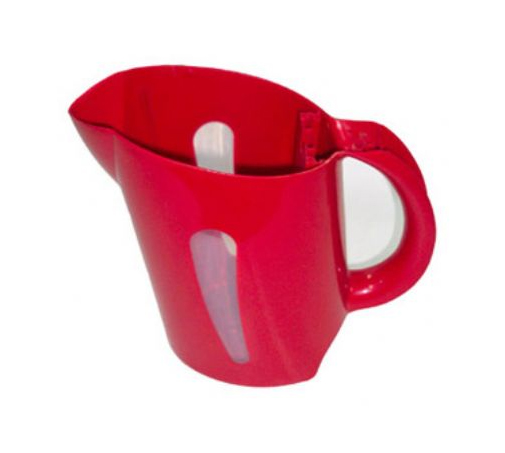
过程中热量的散失是一个我们必须要考虑的一个重要方面,通常热量的散失是由于其传递的不间断性造成的。在注塑生产之时热的传递方式主要有辐射、对流和传导三种,除了大部分被模具吸收之外,还有一部分是通过辐射、对流的方式散发到空气之中的。在模具成型的时候需要提高热量的利用率,而在成型冷却的时候,则需要较快的降低温度,这个就需要冷却模具上战场了,通常冷却采用的介质是水,缘由是水价格低,成本自然也就低,冷却过后的水源可以循环利用。但是毕竟凡事都有利有弊,低价格与可循选使得其只能作为初级冷却剂来使用,如果想要达到佳冷却效果还是需要冷模上场的,在这里需要特别提醒的一点是并不是冷却剂越冷越好,物极必反,过冷可能会出现反效果。
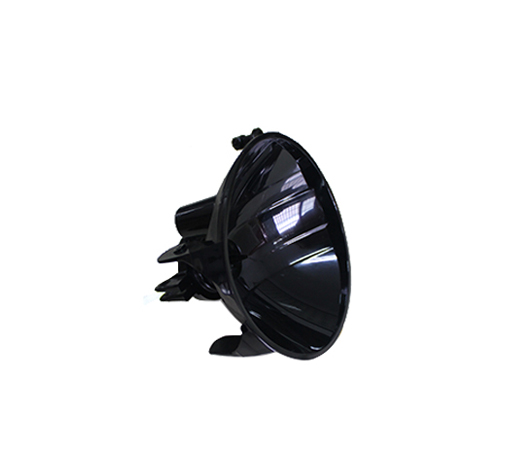
我们的日常生活中使用的是非常多的,对于很多用户来讲对于这些的材料也是比较熟悉的,之前这类产品一直按照一个方向去进行发展,但是社会在进步,行业的发展也需要有相应的变通,也就是我们所说的转型。接下来还要做到让消费者更清晰的认识该品牌、爱上该品牌甚至忠诚于该品牌,这才是常州塑料制品品牌稳步全面繁昌的正途。这才是常州塑料制品厂家建立与消费者精神交互的核心基础。内部首先要变现在单打独斗为抱团作战,通过资源的整合,集中火力去研究用户,强化其在大众市场上的品牌影响力。这样的产品转型是非常重要的,正确的转型可以提高产品的销售量,而且也可以让相关行业发展的越来越好。对于消费者来讲产品转型之后可以为用户提供更多的便利。
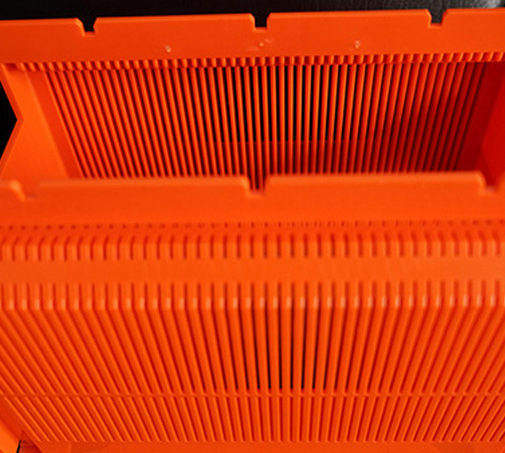
所以必须合理地安排注射、保压和冷却时间,采可以实现注塑加工产品质量和生产率的提高。我们的所说的冷却时间,指的是塑料熔体从充满注塑模具型腔起到可以开模取出制件时止的这一段时间。可以开模取出制件的时间标准,常以制件已充分固化,具有一定强度和刚性为准,在开模顶出时不致变形开裂。即便是用同一种材料进行注塑加工,它的冷却时间也随壁厚、熔融塑料的温度、成型件的脱模温度及注塑模具温度等因素的变化而不同,所以要想百分之百正确地计算出冷却时间还是有一些难度的,只能在适当假定的基础上进行计算。冷却时间有三种参考标准,一种是注塑加工件壁最厚部位中心层的温度,冷却到该塑料的热变形温度以下所需要的时间;另一种是注塑加工件断面内的平均温度,冷却到规定制品的出模温度所要的时间。注塑加工的冷却时间还可以以结晶性塑料成型件壁的厚部分中心层温度为标准,冷却到其熔点以下所需要的时间,或达到规定的结晶化百分比所需的时间。